Ontwerp en fabricage van warmtewisselaars krijgt make-over
Compacte warmtewisselaars, die warmte van het ene medium overdragen naar een ander medium, hebben vele en uiteenlopende toepassingen. Van luchtbehandelingsinstallaties over energieconversiesystemen tot het koelen van micro- en vermogenelektronica. Zowel op het gebied van energie-efficiëntie als op de manier waarop ze worden ontworpen en gefabriceerd, is er echter nog veel winst te behalen. Precies dat is de ambitie van het IAMHEX-project, waarbij met onder meer innovatieve ontwerpsoftware en 3D-printing het de ambitie is om die winst te realiseren.
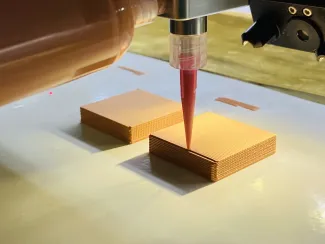
Op het vlak van de energie-efficiëntie van compacte warmtewisselaars, dus van de overdacht van warmte van het ene naar het andere medium, is nog een verbetering mogelijk, ruw geschat van 15 à 30 procent. Dit kan zonder de warmtewisselaar groter te maken of het drukverschil (de drukval) te verhogen, wat niet wenselijk is voor de meeste toepassingen. Althans, die efficiëntiewinst is mogelijk in theorie, want ze ook realiseren ligt niet meteen voor de hand. Dat komt doordat warmtewisselaars, ook compacte, nog veelal worden geproduceerd met klassieke methoden gebaseerd op mechanische productietechnieken. Daardoor is de ontwerpvrijheid van bijvoorbeeld de cruciale vinstructuren die de oppervlakte voor de overdracht van de thermische energie binnenin de warmtewisselaar vergroten eerder beperkt. Ook het ontwerp van warmtewisselaars kan verbeterd worden. Gedetailleerde simulaties op basis van numerieke methoden kunnen te tijdrovend en duur zijn, en kunnen leiden tot ontwerpen die niet maakbaar zijn. Heuristische (probleemoplossende) modellen daarentegen kunnen de ontwerpfase verbeteren maar enkel in bepaalde omstandigheden.
Energie- en materiaalonderzoek
De ontwerpvrijheid wordt veel groter als er niet met klassieke productiemethoden maar met 3D-printing wordt gewerkt. Het is een van de strategieën waarmee binnen het IAMHEX-project de optimalisatie van compacte warmtewisselaars wordt bestudeerd. Het driejarig project gecoördineerd door KU Leuven is gestart in januari 2022 en wordt gefinancierd vanuit VLAIO. Het gaat om breed basisonderzoek uitgevoerd binnen de intercluster-samenwerking, wat inhoudt dat verschillende wetenschappelijke disciplines betrokken zijn, in dit geval energie- en materiaalonderzoek. Van beide projectpartners – KU Leuven en VITO – werken daarom zowel energie-experts (EnergyVille) als materiaalexperts aan het project mee. Het project kadert binnen de Vlaamse energiecluster Flux50 en de materialencluster SIM Flanders.
Binnen het project wordt ingezet op additive manufacturing via 3D-printing met koper en aluminium. Het printen gebeurt met twee verschillende technieken: Laser Poederbed Fusie, waarin KU Leuven is gespecialiseerd, en 3D micro-extrusie, waarin VITO is onderlegd. ‘Beide technieken hebben hun voor- en nadelen’, zegt Johan Van Bael van VITO/EnergyVille. Bij de eerste wordt het metaal in poedervorm door laserlicht tot smelten gebracht. Bij de laatste wordt er geprint met een viskeuze pasta gevuld met metaalpoeder (bv. koper of aluminium legeringen), waarna een thermische behandeling volgt en er quasi zuiver metaal overblijft. Met de 3D-printingtechnieken wordt onder meer onderzocht hoe de functionaliteit van de warmtewisselaar kan worden geoptimaliseerd op het vlak van warmtegeleidbaarheid en mechanische sterkte, hoe het oppervlak van de vinnen gladder kan worden gemaakt maar ook hoe er met hoge precisie en ontwerp vrijheid kan worden gefabriceerd. Bedoeling is om de prototypes van een compacte warmtewisselaar te testen op twee niveaus: op micro-schaal en op reële schaal.
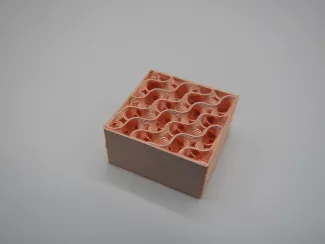
Alles komt samen
Het IAMHEX-project focust niet alleen op nieuwe fabricagemethodes voor compacte warmtewisselaars. Ook het ontwerpgedeelte krijgt veel aandacht. ‘Met geautomatiseerde ontwerptools willen we het design optimaliseren’, vervolgt Van Bael. ‘Zo willen we innovatieve software ontwikkelen waarbij algoritmes de optimale configuratie bepalen. Dat kan tijd en dus kosten besparen.’ Opnieuw voor de vinnen zou dat concreet inhouden dat de computer hun vorm en positionering binnen de warmtewisselaar optimaliseert, dit op basis van randvoorwaarden ingegeven door de ontwerper.
Binnen het ontwerpgedeelte wordt ook de maakbaarheid, en vooral de beperkingen daarin, bestudeerd. Het heeft immers geen zin om de perfecte warmtewisselaar op de computer te ontwerpen als die niet in die vorm kan worden gefabriceerd.
De ambitie van het project schuilt in de brede focus, op zowel het ontwerp als de fabricage van compacte warmtewisselaars, die beide een make-over krijgen. Van Bael: ‘Doordat we innovaties onderzoeken op het vlak van zowel ontwerpsoftware als op vlak van productietechnieken, komt alles samen.’ De hoop en verwachting is dat de projectresultaten een revolutie teweeg zullen brengen in het ontwerp en de fabricage van dit soort warmtewisselaars – waarbij de beperking in volume maakt dat er vernuftiger moet worden geïnnoveerd.
Door het basiskarakter van het onderzoek leent IAMHEX zich voor verdere valorisatie van de resultaten. Daarvoor wordt een roadmap ontwikkeld. Het project mikt door dat karakter ook niet op de realisatie van een kant-en-klare warmtewisselaar of van gebruiksklare ontwerp-software. Wel kunnen met bedrijven gespecialiseerd in het ontwerp en de productie van warmtewisselaars vervolgtrajecten worden opgestart.
Maar ook buiten de wereld van de warmtewisselaars zijn er valorisatiemogelijkheden. ‘De 3D-printing-techniek met koper en aluminium legeringen kan ook heel interessant zijn in andere toepassingen, bijvoorbeeld in de fabricage van componenten voor elektrische machines’, aldus Van Bael. Innovaties uit het project, zoals de pasta en het fabricageproces voor 3D micro-extrusie, kunnen zo hun weg vinden naar concrete toepassingen in de bedrijfswereld.