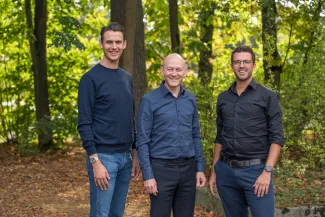
VITO Venture Studio
The VITO Venture Studio is a programme within the Tech Transfer Office (TTO) that is solely designed to create and launch new spin-off ventures. Our mission is to empower scientists, intrapreneurs, and entrepreneurs to transfer VITO technology to industry, in order to bolster the Flemish economic fabric by creating spin-off ventures. We strongly believe that in supporting innovation and entrepreneurship, we contribute to a better future for the wider society.
Our portfolio criteria
We are driven by a vision of unleashing the potential of new spin-off ventures that can transform and have a positive impact on the world. To achieve this impact, we focus on four key elements that are essential for success:
- Passion: We are passionate about finding and nurturing the best ideas that can solve real problems and create value for society.
- People: We empower and attract talented and diverse teams that share our vision and values, and provide them with the resources and support they need to thrive.
- Technology: We leverage the power of technology and innovation nurtured at VITO, to create cutting-edge solutions that can scale and adapt to changing needs and markets. We are always on the lookout for new ways to enhance our products, services, and processes with the latest tools and techniques.
- Growth: We aim for exponential growth that can attract external financing and partnerships that can help us expand our reach and influence. We are not afraid to think big and pursue ambitious goals that can make a difference in the world.
The process
Once the Tech Transfer Office identifies promising VITO technology, we begin the development process of actual spin-off ventures. The incubation process involves:
- Matchmaking between technology and market
- Preparing a business and financial plan
- Team creation process
- Entrepreneur-in-residence programme
- Maturing the technology
- Mentorship
- Network capacities
- Securing external investors
- IP and legal counseling
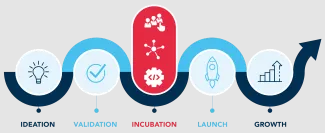

Currently incubating: Pleevi
Pleevi offers the ‘Smart’ in Smart Charging to electrical integrators and operators that help companies enter the electrical era. Our SaaS solution makes electrical site hardware such as charging points, storage solutions and solar panels truly smart.
Would you like to know more?
Curious about the activities of the VITO Venture Studio and our spin-offs? Contact Nils Wuytens for more information.