Flash calcination for Belgian cement substitutes production
Cement and concrete are the backbone of infrastructure worldwide. The downside is the climate impact these products have. Part of the solution to cement's climate challenge lies in the use of cement substitutes. A promising and local source of cement substitutes is clay-based dredging sludge. VITO is building a Flash-Calciner pilot installation to convert these and other clay-containing streams into functional cement substitutes. This new infrastructure will allow the cement and concrete industry to experiment with these new raw materials for cement.
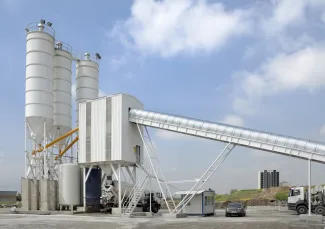
Towards a CO₂-negative cement industry
Bridges, tunnels, roads and apartment buildings: all are built from concrete. Of all man-made materials, concrete is by far the most widely used and produced material. However, the production of cement for that concrete is linked to large emissions of CO₂, with an European average of almost 700 kg per tonne of cement. Although the embedded CO₂ per tonne is well below that for steel production and several orders of magnitude lower than plastic, cement production contributes almost as much to total CO₂ emissions as the steel industry and many times more than the chemicals sector. This is purely due to the gigantic scale of cement and concrete use.
To help halt global warming, the cement industry has developed a roadmap under which the sector aims to become CO₂-negative by 2050. One of the action points of that roadmap focuses on cement composition modification. Modifying cement composition with cement substitutes could reduce the CO₂ impact of cement by 10% per tonne at EU level. This makes it one of the most impactful technologies.
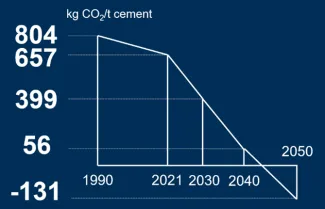
A new kind of cement substitute is needed
Cement substitutes are substances that can replace Portland cement without negatively impacting concrete properties. Blast furnace slag and fly ash have been used for years as cement substitutes for the production of CEM II and CEM III. However, the production of these material streams is under pressure due to the climate ambitions of both the steel industry and energy production. The steel industry is betting on new types of furnaces and techniques (electric arc furnace and direct reduced iron), leading to different compositions of slag compared to blast furnace slag. The phasing out of coal-fired power plants in Europe will also put an end to fly ash, which is currently used as a cement substitute. Meanwhile, in Belgium, the last coal-fired power plant has already closed. There are also natural raw materials that can serve as cement substitutes, such as volcanic ash or natural zeolites, or natural materials that acquire reactive properties as cement substitutes after heating at 700-900 °C, such as kaolinitic clay. However, such raw materials hardly occur in Belgium in volumes relevant for cement. So there is a need for new types of cement substitutes, preferably locally available.
In 2020, VITO, commissioned by OVAM, conducted a screening of potential Flemish waste streams that could be used as cement substitutes. In addition to the quantities of available material, the potential risks that could arise from its use were also examined. The presence of heavy metals in non-ferrous slag and bottom ashes from domestic waste incineration, for example, means that these streams have lower potential. The ceramic, stone and porcelain fraction released from glass upgrading has technical potential, but the amount released annually is too small to be relevant. The fine fraction released from concrete rubble crushing does have high potential and it has already been included in the new standard EN 197-6, although several avenues of research are still being pursued to increase the reactivity of the material.
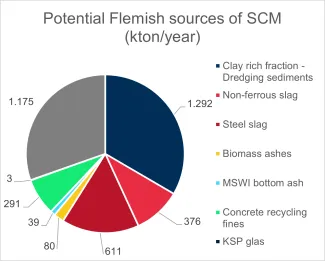
The potential of clay-rich dredging sludge
A large promising stream that remains is the clay-rich fraction of dredging sludge that is dumped annually. In recent years, VITO has conducted intensive research commissioned by the Flemish government to activate this material stream into a suitable cement substitute. Dredging sludge from the port of Antwerp is treated by the Maritime Access Department at the AMORAS site. The sand is removed and made available as construction sand, while the clay-rich fraction is pressed into filter cakes that are stored on an adjacent site. The filter cakes have a fairly constant composition, which is ideally suited for conversion into a cement substitute by heating. Research shows that flash calcination, in which the filter cakes are dried and pulverised, then heated briefly (~2 seconds) to 850°C, leads to a cement substitute whose reactivity is similar to that of the better fly ash. The relationship between phase transformations and reactivity is being investigated in projects such as HEU ROTATE and CLEI.
Tests at mortar level show that replacement rates of 30 gew% based on CEM I result in 90% relative strength development compared to the 100 gew% CEM I reference mix after 28 days. This lends to the possibility of developing 42.5-52.5 N cements with a clinker content of < 70 gew%.
Following this research, the Maritime Access Department will offer interested parties full access to the research results, and in 2025 an open call will be launched for the off-take and possible construction of a first full-scale calcination plant in Flanders for the valorisation of dredging sludge.
Unique research infrastructure for industry: the Flash-Calciner
VITO, meanwhile, with the support of EFRO, is expanding its research infrastructure with a flash-calciner. This open pilot installation will
-
offer the cement and concrete industry the opportunity to experiment with different calcined streams
-
offer holders of clay-based waste streams the option to easily check whether their stream can be upgraded to a cement substitute
-
allow researchers to optimise and objectively evaluate the flash calcination process.
The installation will be equipped with a pre-heater and calciner loop of over 20 metres, made of refractory material. This will ensure a dwell time of 2 seconds at a constant temperature gradient, with a feed rate of 25 kg/h.The plant will also be equipped with a colourcontrol system.
This option enables us to adjust the temperature during the cooling phase, allowing us to adjust the colour of the calcined material. Without this option, the clay will often turn red; using the colourcontrol, we can also give the materials a grey colour, which is closer to that of cement. With this, the pilot plant has all the components that are also present in a full-scale plant, so materials can be tested under real conditions.
In addition, the installation will be equipped for emission measurements, so that we can also assess any emission control measures needed in a full-scale installation. Of course, the installation is equipped with a filter system, so that we do not have a negative impact on the environment even during small-scale tests.
The contract to build the Flash Calciner was awarded to Equans and its subcontractor FCT International in August. Detailed plans are currently being worked out. Construction of the plant at Equans' site in Zwijndrecht will start in spring 2025. In autumn 2025, the plant will be brought to VITO in Mol and installed next to the new VITO Earth building. The opening of the pilot installation is planned for spring 2026.
Contact us
Expert Circulaire Cementvervangers
Projectcoördinator
