Produce more with less, thanks to membrane technology
Continuing to produce top quality pharmaceutical drugs and fine chemicals while limiting costs and energy consumption is a challenge that VITO is addressing, alongside the pharmaceutical and fine chemicals industries. VITO develops practical solutions to improve industrial processes. With sustainability as the guiding principle, and cost reduction, energy saving and higher product yields as outcome.
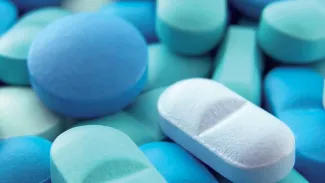
To remain profitable, the chemical and pharmaceutical industries must undergo a process of reinvention. VITO develops technologies that accelerate this process. We focus among other things on process intensification, making processes more efficient and more sustainable. In this, low consumption of energy and other resources are an absolute necessity.
Process optimisation 2.0
Of course, these industries have progressed during the past few years. Many companies have already invested heavily in process optimisation. They look for disruptive solutions that outperform the traditional chemical methods: process optimisation 2.0, as it were. VITO offers innovative technologies and state-of-the-art test infrastructure at lab and pilot scale and conducts techno-economic feasibility studies. As a neutral research partner, we are able to give objective advice, independent of third parties. Our customers also benefit from our extensive network in the research community and industry. They gain access to complementary expertise and collaboration.
Different needs per player
VITO targets R&D players as well as manufacturers. R&D players aim at the shortest possible time to market, a higher success rate and higher performance. When they encounter technical problems such as process inhibition, they can come to us. For one R&D company, we are for example investigating the enzymatic synthesis of an industrial protein. Organisations that manufacture for pharmaceutical companies on a contract basis can also call on VITO, for example, to reduce their production costs without sacrificing product quality. Looking at it this way, they too are focused on innovation. Large pharmaceutical companies are driven to innovation by time to market and the need to reduce production costs. VITO provides solutions for these challenges, such as our patented VID® technology.
50 to 90 % lower energy costs
Industrial processes often involve complex separation steps in which components are isolated, purified or concentrated. On the one hand, VITO offers solutions for downstream processing in which target molecules are purified to a final product in successive steps. On the other hand, VITO works on the integration of separation and conversion. In each case, membranes are key to reducing energy costs. Traditional separation processes absorb energy: from 40 to as much as 70 % according to a detailed study of industrial chemical processes. In comparison with conventional processes such as evaporation and distillation, membranes are much less energy-intensive, since the separations generally occur in room temperature, without the different components undergoing a phase transition. Thanks to membrane technology, energy costs can be reduced by 50 to 90 %. Moreover, higher product quality can be obtained for temperature-sensitive molecules. Organic Solvent Nanofiltration (OSN) is an interesting example of the evolution in membrane technology that is contributing to sustainable chemical processes. The compactness and the possibility of scaling up a modular system are also major industrial benefits of membranes.
Functional membranes
And development continues. Together with the University of Antwerp VITO has developed a new generation of functional membranes with the patented FunMem® platform. FunMem® allows separations to be performed based on affinity, not just size. Specific organic groups applied to the surface of ceramic membranes make the membrane functional. An interesting application is the removal of impurities from Active Pharmaceutical Ingredients (APIs). Another example is the separation of catalysts from the production process, so that they can be reused. For example, we succeeded in recovering the expensive noble metal palladium, a widely used catalyst in the chemical industry.
Optimization with VID® technology
So-called substrate inhibition occurs in certain chemical reactions. When this inhibition of the process takes place, high concentrations of substrate can lead to the formation of undesirable by-products, with reduced yield and lower product quality as a result. For this reason, companies prefer to perform these vulnerable reactions in a highly-diluted medium. This has a major disadvantage: you need large quantities of solvent and bulky reactors to create small amounts of a final product, for example 6 000 litres of solvent for only 50 kilograms of product. VITO’s patented VID® technology (Volume Intensified Dilution) integrates membranes directly in the process, so that more product can be made with smaller reactors and less solvent. VID® makes inhibited reactions much more efficient by reproducing a diluted reaction mixture in a smaller reaction vessel. Sending the reaction mixture over a membrane allows the solvent to be reused. Some reactions benefit from efficiency increases of more than 80 %.
Cheaper with FUNMEM® membranes
Chiral molecules have two forms: they look the same, but in fact are each other’s mirror image. But this distinction is crucial. One form has the desired therapeutic effect, while the mirror image can result in life-threatening side effects. Traditional chiral separation is done using chromatography, but this is expensive and time consuming, uses a lot of solvent and is detrimental to the environment. We are now examining whether we can perform chiral separations using FunMem® membranes. A test case for chiral amines has already shown that membrane separation is economically viable if we combine the right membranes. It’s promising for the pharmaceutical and chemical industry.