SolTex: Solvent recovery for textile recycling
SolTex aimed to develop a circular resource optimisation in the frame of a Danish, mixed textiles fibre-to-fibre recycling project. The SolTex project focused particularly on solvent recovery and re-use.
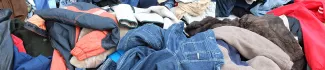
Textile industry creates about 10% of the green house gas emissions, and is responsible for very high water consumption (~2700 L per cotton shirt). Moreover, a huge amount of textile waste - about 92 million tons - is produced annually. Currently, only 1% of the textile is recycled, and more than 50% is incinerated or ends up in a landfill.
To incentivize a more sustainable textile industry, worldwide different legislative and technological initiatives are taken. In Europe, the EU directive 2018/851 mandates separate collection and recycling by 2025. Furthermore, a multitude of technology development projects are funded, searching for energy and resource efficient recycling processes.
Typically, sustainable textile recycling asks for a complex combination of mechanical and chemical processes, taking into account the circular resource optimization of all auxiliaries required. In the chemical processes this asks e.g. for efficient recovery of the solvents typically used for fibre dissolution.
Dimethyl sulfoxide recovery and reuse with ceramic membranes
SolTex focused on one core component of the overarching Danish textile recycling project: solvent recovery and reuse - and more particularly the recovery and reuse of the solvent DMSO (dimethyl sulfoxide). DMSO recycling has great commercial potential in the textile recycling project itself, but also in general. The SolTex project partners studied recycling DMSO with membrane technology in particular, as energy consumption of traditionally used distillation is not sustainable. The use of ceramic membranes in the DMSO process is considered the best option, in view of membrane durability and the high treatment temperature (90°C). To guarantee good removal of dye components, specifically commercially available ceramic nanofiltration membranes were tested. These can be native membranes, or newer Grignard grafted for better solvent performance. The grafting method was already developed and upscaled by INNOMEM partner VITO (INNOMEM Pilot Line 3), and the resulting membranes recently entered the market.
SolTex identified the optimal membrane and membrane process, performed proof of concept at intermediate scale. Subsequently, it performed a first valuable Techno Economic Evaluation allowing to define the next step for piloting and upscaling of the process.
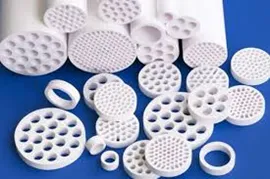

DMSO recycling with membranes reduces costs
Three types of ceramic nanofiltration membranes, native and grafted versions, were selected for screening testing. The results showed that all membranes were able to remove the dye impurities by at least 85%, creating a clear, color-less DMSO permeate. The best membrane was chosen based on the combination high flux + high retention.
Subsequent Proof of Concept testing with a multichannel membrane (0.1 m2 membrane area) showed the feasibility to recycle at least 90% of the solvent, with relative low flux decline during the concentration process. Optimal process parameters were defined, and extra tests revealed an efficient process to clean the membrane, ready for re-use.
Based on the flux results obtained, an economic analysis was performed allowing to deduce that the cost of the membrane-process to recycle DMSO is far lower than the purchase cost of new DMSO. A large amount of purified DMSO was sent to B4C to check re-use.
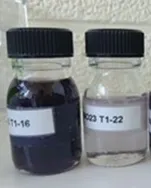

Flux track during concentration up to 95% DMSO recovery
SolTex project conclusions
The SolTex project was successful and the following conclusions can be drawn:
- Tight ceramic membranes (commercially available from INNOMEM partner RKV) remove the dye impurities from the DMSO process streams originating from textile recycling, up to 90% (KPI1).
- Proof of concept testing at intermediate scale of membranes, proved the feasibility to recover the DMSO up to 90% (KPI2).
- The process fouls the membrane but a relative mild cleaning can recover its process flux up to 100% (KPI3).
- A first detailed Techno-Economic Assessment revealed a DMSO recovery cost way lower than the purchase cost of new DMSO.
Techniques used in SolTex
In the SolTex project the following services and capabilities of the INNOMEM OITB were used:
- Grafting of ceramic nanofiltration membranes, feasible at INNOMEM partner VITO.
- Screening and Proof of Concept testing of ceramic nanofiltration membranes with solvent-based streams at high temperature, requiring specialized filtration equipment at lab and pilot scale, available at INNOMEM partner VITO.
- Techno-economic Assessment of membrane processes, available within the INNOMEM OITB, and here performed by partner VITO.