Solvent based membrane nanofiltration for process intensification
Organic solvent nanofiltration (OSN) is an emerging technology since it offers an economically interesting alternative separation process that has the added advantage of often leading to a more sustainable process. Allowing non-thermal, energy efficient and highly-selective separation, OSN has the potential to replace part of the huge number of traditional, mainly thermal separation processes currently used in the chemical and pharmaceutical industry.
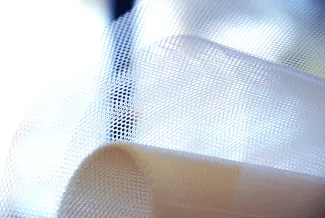
Until about 10 years ago, it was hardly possible to treat organic solvent-based solutions with nanofiltration due to the lack of solvent-stable membranes and in-depth knowledge of processing such streams. However, currently several high-performance OSN membranes exist, both polymeric and ceramic at a sufficient level of development and commercially available. In order to profit from the full potential of OSN, some remaining challenges and market demands need to be solved. One of these important market demands is more extensive demonstration of the technology by relevant pilot testing. Testing the various applications at pilot scale is a must, since it is common practice that end-users only choose for new developments that have already been implemented at reference sites, or at least technically proven at larger scale.
Pilot scale OSN installation
Nowadays, some OSN pilot test facilities exist with current membrane suppliers. However, to facilitate independent pilot-testing for potential end-users, VITO has designed and recently acquired a large-scale nanofiltration installation suitable for use with virtually all organic solvents (full installation ATEX EEx IIB T4).
Recognising the enormous potential of the new technology for the pharmaceutical and fine-chemical industry (see Section 3), the installation was designed to meet the good manufacturing practice (GMP) requirements imposed upon pharmaceutical manufacturing: apparatus and components meet the required high quality levels with respect to cleanability (fully drainable and cleaning in place possible), materials (AISI 316L), surface roughness (Ra= 0.8 lm), certification, etc.
Furthermore, to avoid any restrictions of membrane choice, the equipment allows for the use of both ceramic membranes (3 × 19 channel elements with a length of 1.2 m, total membrane surface 0.75m2) and polymeric membranes (1 × 4-040 inch spiral wound module with a diameter of 4 inch and a length of 40 inch, total membrane surface about 6m2), both under optimal conditions. Especially this compatibility with both ceramic and polymeric membranes is a unique feature of this installation.
A simplified flow sheet of the pilot is shown in Fig. 1. The installation is built following the usual two-pump design. The solvent is pumped out of a 400 L tank by a high pressure pump up to the working pressure and is circulated by a circulation pump at high flow rate (adjustable) over the membrane module (cross flow operation). The dedicated feed tank of 400 L allows for inert gas blanketing and is instrumented to monitor temperature, pressure, and liquid level. Two spray heads allow for efficient cleaning. The main technical characteristics of the installation are summarised in Tab. 1.
Parameter | Pilot specification |
Operating pressure |
0-45 bar |
Maximum temperature |
50°C ATEX, 80°C non-ATEX |
Maximum feed volume |
80 L |
Maximum circulation flow |
7000 L h –1 |
Maximum permeation flow |
500 L h –1 |
Skid dimensions |
Skid1: 2.6m x 1.5m x 1.9m |
(length x width x height) |
Skid2: 1.2m x 1.2m x 2.5m |
The installation is connected to a computer for real-time monitoring and data acquisition (pressures, temperatures, tank level, cross-flow velocity, and flux). Sampling points for tank outlet, permeate, and retentate are foreseen since no inline analysis is available. The pilot was designed to be mobile (two transportable frames) and can be rented for testing either at VITO or on-site at the end-user.