Successful API recovery from a distillation residue at SITECH-DSM
The growing acceptance of membrane technology in industry and the availability of more and better membranes in recent years have increased interest in using membranes also in organic solvent streams.
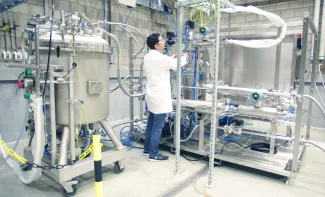
As new membranes are able to separate organic mixtures at the molecular level, a wide variety of downstream or in-process applications become possible: e.g. purification of target compounds, recovery of expensive homogeneous catalysts, product fractionation, exchange of reaction solvents. Also on the level of process development, significant efforts are being devoted to the development and demonstration of novel solvent based membrane processes, several of which have been implemented at industrial scale in the meantime.
Thanks to its wide applicability and non-thermal, and therefore energy-efficient and mild character, organic solvent nanofiltration (OSN) is rapidly becoming a valuable part of the separation specialist’s toolbox in the fine chemical, pharmaceutical, food, biotechnology and related industries. Being one of the companies taking sustainability and innovation seriously, Sitech-DSM in Venlo decided to explore the potential of OSN for the recovery of a valuable API from a methanol-based distillation residue.
Lab-scale feasibility tests at Sitech-DSM
To determine the feasibility of the API recovery using OSN, a series of lab-scale tests were performed at Sitech-DSM. At first, several commercially available membranes were screened in order to determine the optimal membrane. Membrane criteria were: low, preferably zero retention for the API, high retention for the tar impurities in the residue and high permeate flux. Subsequently, tests were performed with a small-scale spiral-wound module of the membrane of choice.
This way, the optimal process parameters were determined. The preferred process consisted of a concentration step (10x), followed by a diafiltration using 3 diavolumes of methanol. Longer term tests allowed a first assessment of the stability of the membrane and module components in the methanol-based distillation residue. After this successful lab-scale tests, the batch-wise processing of the existing quantity of distillation residue was performed at pilot-scale, using the GMP-compliant pilot equipment of VITO.
GMP-compliant OSN pilot
Recently, VITO has designed and acquired a large-scale mobile pilot installation for OSN, to facilitate the transfer of this new promising technology for process intensification to industry. The installation, suitable for all requirements ranging from proof of principle testing to pilot scale production, is mobile and can be equipped both with ceramic (3 x 19 channel elements of 120 cm ~ 0.75 m2) and polymeric membranes (1x4 inch module ~5 m2). The pilot is full explosion proof (Atex), and meets the regulatory requirements of pharmaceutical and fine chemical manufacturing (GMP: good manufacturing practice). The installation is available to customers on a rental basis. Testing can be done either at VITO or on-site at the end-user.
Figure 1 shows a picture of the pilot in operation at VITO. The installation consists of 3 mobile parts: a skid with the membrane modules, pumps, electrical control box and data acquisition system, a dedicated 400 l feed tank foreseen with the necessary monitoring instrumentation and a separate skid with a transfer pump and for the N2 blanketing. A more detailed description of the technical characteristics of the installation can be found in 'Solvent Based Membrane Nanofiltration for Process Intensification' [1].
On-site API recovery
For the project at Sitech-DSM, the VITO pilot was operated on-site in Venlo, with shared pilot supervision. In total 52 batches containing each 250 kg of valuable API were successfully processed over a period of 6 months. During this period the pilot ran continuously 24 hours a day, 7 days a week, with minimal man power, and without any serious problem. Figure 2 shows a picture of the pilot running on-site at Sitech-DSM. The project allowed Sitech-DSM to recuperate > 10 tons of the valuable API, making the innovative OSN process very cost-effective.
[1] A. Buekenhoudt, H. Beckers, D. Ormerod, M. Bulut, P. Vandezande, R. Vleeschouwers, “Solvent Based Membrane Nanofiltration for Process Intensification”, Chemie Ingenieur Technik, 2013, 85, 1-6.