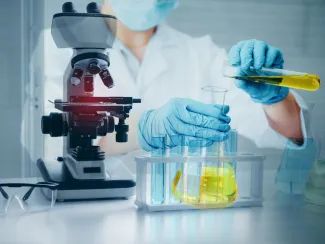
Our products & services
Are you looking for a product or service that can help you in your transition to a sustainable way of working? In this overview you will find a selection of what we do. On the left, you can filter the applications according to your areas of interest. Would you like to know more about a particular technology? You'll find the right contact person on the details page of each application.