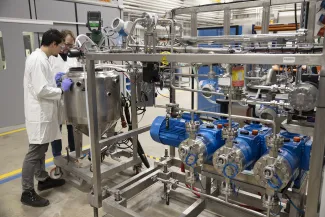
Water membrane filtration pilot units
At VITO we offer a range of pilot scale solvent membrane filtration equipement which uses organic solvent based pressure-driven membrane filtration. The units can be used for a wide range of applications such as concentration, purification and solvent swap of APIs or clean-up of viscous waste oils, plastic oils, lignin oils, etc.
What can you use them for?
- Concentration, purification and fractionation of target compounds from water-based process streams
- Concentration, purification and fractionation of water-based extracts of natural compounds
- Recovery of water, valuable compounds and lye from underutilised by-products or food production by-products
- Wastewater treatment
- Recovery of target compounds from sugar co-products
- Purification and concentration of target compounds from water streams
- Recovery of water from co-products and wastewater
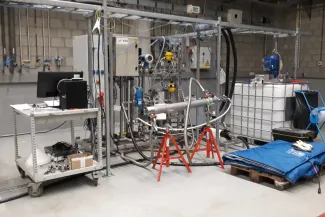
MFU40-5 Pilot
Technical features:
- Mobile cross-flow pilot unit for water-based pressure-driven membrane filtration (MF, UF, NF, RO)
- Max. 80°C – 40 bar (316 L, Viton)
- Multi-channel ceramic membranes, 4040-type spiral-wound elements and tubular polymeric membranes
- Various feed tanks available, min. working volume 25 L
- Semi-automatic operation, fully instrumented with real time process monitoring and data acquisition
- Non-food grade (open) installation, applicable for food/pharma applications through disinfection protocol
Reference industrial show cases:
- Purification and concentration of oxidized lignin
- Concentration and purification of sugar side-streams
- Desalting of modified natural product for cosmetics application
- Valorization of side stream from citric acid production
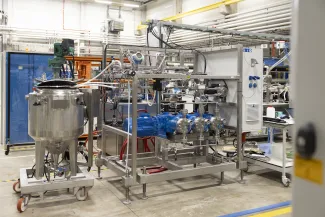
Sanitary NF pilot
Technical features:
- Skid-mounted (semi-mobile) small cross-flow pilot unit for water-based pressure-driven membrane filtration (MF, UF, NF, RO)
- Sanitary/hygienic design specifically meant for water-based food/pharma streams
- Max. 80°C – 40 bar (316 L, Viton)
- Only 2540-spiral-wound elements currently, extension to multi-channel ceramic membranes planned
- Various feed tanks available, min. working volume 20 L
- Semi-automatic operation, fully instrumented with real time process monitoring and data acquisition
Reference industrial show cases:
- Fine-separation of sugar syrup
- Desalting of modified natural product for cosmetics application
- Downstream purification of target compound from fermentation broth
- Clean-up of side-stream from sugar manufacturing plant
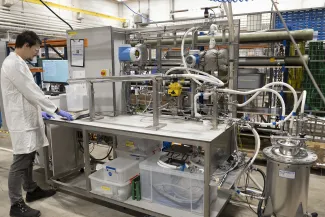
MFU60-1 Pilot
Technical features:
- Skid-mounted (semi-mobile) small cross-flow pilot unit for water-based pressure-driven membrane filtration (MF, UF, NF, RO)
- Max. 80°C – 60 bar (316 L, Viton)
- Multi-channel ceramic membranes, 2540-spiral-wound elements and tubular polymeric membranes
- Various feed tanks available, min. working volume 5 L
- Semi-automatic operation, fully instrumented with real time process monitoring and data acquisition
- Non-food grade (open) installation, applicable for food/pharma applications through disinfection protocol
Reference industrial show cases:
- Purification of modified lignin from alkaline crude liquor
- Recovery of valuable oligosaccharides from underutilized sugar side-streams
- Downstream purification of target compounds from fermentation broths
- Clean-up of side-streams from metal recovery processes
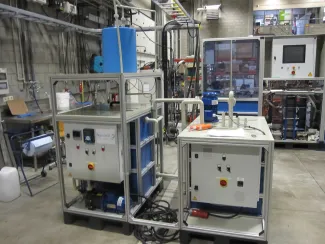
Membrane contactors pilot
Technical features:
- Small MD pilot in AGMD configuration
- Standard module: 7,2 m² spiral-wound
- Heating capacity 18 kW, cooling capacity 1,2 m³/h (@ 4,14 bar water pressure)
- Max heating temperature: 85°C
- Feed tank of 250 L
- Continuous logging of temperatures, pressures and distillate production
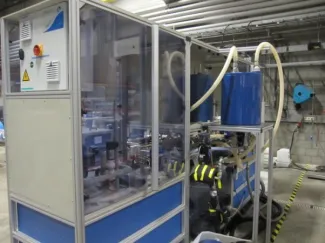
Membrane distillation pilot unit - MD pilot 1
Technical features:
- Skid-mounted, semi-mobile MD pilot which can be used in DCMD and AGMD configuration
- Standard module: spiral-wound, max. 3 modules in parallel
- Feed and brine tank of 280 L
- Max temperature: 85°C
- Conductivity measurement brine: 0,5 – 500 mS/cm; distillate: 5 – 5000 µS/cm
- Expected distillate production: 7 – 100 l/h depending on process conditions
- Fully instrumented with real time process monitoring and data acquisition