Carbstone technology fundamental to sustainable construction
It is in our mission statement: VITO wants to facilitate and accelerate the transition to a sustainable world. The patented Carbstone® technology ensures that one of the major stumbling blocks in this transition - CO2 - is stored in building materials in a circular way. Limburg-based Orbix and building materials manufacturer Masterbloc have now industrialised this Carbstone® technology and the first circular sustainable indoor wall bricks are a reality.
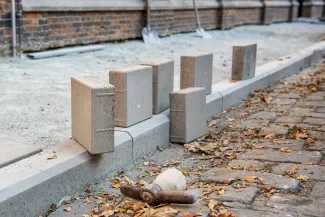
The greatest inventions often come about by chance. So too with Carbstone. Over 18 years ago, VITO was involved in an Orbix project looking at how steel slag could be used as a covering layer for landfills. VITO experts noticed that the steel slag became rock-hard during accelerated ageing tests in a CO2 atmosphere.
A discovery that immediately got the greatest attention from Orbix R&D manager Dirk Van Mechelen. After all, he had noticed some time ago that steel slag hardens with natural ageing. And Orbix had also concluded that this hardening was caused by the limited presence of CO2 in the atmosphere.
Building blocks of CO2
"I immediately saw an opportunity," says Serge Celis, CEO of Orbix. "A chemist was able to tell me that the cause was the carbonation of certain components of steel slag. So I took one of those CO2 bottles also used in drinking establishments on tap and looked what happened when I passed it through those residual fractions."
The experts at VITO were just as fascinated by this process as Serge Celis and they decided to use the reaction of CO2 with metal slag in a targeted way to produce a building block. "That's all it took to win Mr Celis over. He is not only a driven entrepreneur, but also a man who immediately saw the opportunities of this process," says Mieke Quaghebeur, who led the research for VITO. "It was the beginning of a great collaboration."
Double win
"It is indeed great to work with VITO," Serge Celis proclaimed at the press conference where the building blocks were presented. That collaboration resulted in the patented Carbstone technology in 2011. "We use steel slag as the basis," explained Mieke Quaghebeur. "We combine the steel slag with CO2, causing a reaction between certain minerals in the steel slag and the CO2. The result is the formation of a kind of 'glue' that ensures the strength development and hardening of the bricks. The steel slag captures the CO2, so to speak. This sustainable technology also has the special side effect of eliminating the use of cement. Cement is currently responsible for about 10 per cent of global CO2 emissions. So there is a double win: we use CO2 to make the Carbstone and we avoid CO2 emissions in the production and use of cement."
"This Carbstone technology also makes it possible to make numerous CO2-negative as well as circular building materials, from tiles to clinkers, roof tiles, facade bricks and building blocks. Now that we can make this on an industrial scale, we are building climate-conscious, circular and more sustainable, because the bricks are perfectly recyclable."
CO2 must be limited throughout the process
Yet Serge Celis remains very realistic. "By making these bricks, we create a negative footprint: we take in more CO2 than we consume. But that is only possible if we make sure that no more CO2 is consumed in the entire production process from steel slag to brick, through transport and logistics, for example. That is why I advocate a kind of hub in Genk where all the companies involved are close together..."
That the government also believes in this technology is proven by the renovation of Cofinimmo's office building in Mechelen, which also houses OVAM. This is being constructed with circular building blocks by Mechelen-based construction group Vanhout.
Construction sector wants to be part of the solution
Flemish Environment Minister Zuhal Demir is already completely won over by this process. "The construction sector is responsible for 40 per cent of CO2 emissions," she says. "So it is not too surprising that the Flemish government is mainly looking in the direction of construction companies to look for partners to reduce our emissions. Incidentally, we notice that the construction industry is increasingly looking to become part of the solution itself. Pioneering companies such as Orbix and Masterbloc are outlining the way forward. Technology and development are crucial here. So it is good that VITO's expertise can be used in this respect. They show us the way to a more climate-friendly building sector and a liveable Flanders."
The climate chamber at the Masterbloc site in Maasmechelen is good for a production of some 70 tonnes of CO2-bound building blocks per day or 15,000 tonnes on an annual basis. "But this is only one climate chamber. We therefore want to build additional climate chambers soon to spread this technology as widely as possible."
In doing so, the producers are also looking at customers abroad.