Sustainable recycling of LFP batteries is an environmental and an economic necessity
Decarbonization of society is a fact. Fossil fuels are being replaced by renewable energy. Batteries are crucial for such transition, but they can also be a weak link. They contain critical raw materials, which means that sustainable recycling is necessary. But this is not yet possible on a large scale. The ACROBAT consortium - a collaboration of research institutes and top players - focuses on the recycling of lithium iron phosphate (LFP) batteries. In this way, more than 90% of these critical raw materials could be recycled by 2030, which is important from both an environmental and an economic point of view.
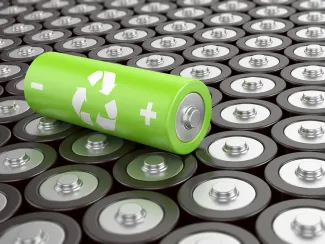
LFP batteries, a specific type of lithium-ion batteries, have a long service life, require little to no maintenance, are extremely safe, light in weight and have improved charge and discharge efficiency. In addition, they do not contain highly expensive metals such as cobalt and nickel, which makes them cheaper than other commercially available lithium-ion batteries. Because of these advantages, they occupy an increasing segment of the battery market. They find applications not only in vehicles, but also in stationary batteries, electrical tools, e-bikes and e-scooters, and household appliances.
Critical raw materials
LFP batteries contain critical raw materials, which are difficult to mine in Europe, but they are crucial for our economy, namely lithium, phosphorus and graphite. Since Europe strives for greater independence of its production processes, it is necessary that we can recycle these raw materials locally from end-of-life batteries. In addition, there are also environmental issues to be considered as these batteries contain polluting substances that could be removed during recycling. However, no specific economical viable recycling process for these LFP batteries exists in Europe on an industrial scale.
In ACROBAT, the Belgian VITO, and the SIM2 Institute of KU Leuven, the German Fraunhofer ILT, the Italian ENEA and the German battery recycling company Accurec Recycling GmbH will develop innovative and environmentally friendly processes and separation techniques for end-of-life LFP batteries. In this way, a considerable amount of critical raw materials can be recovered and reintroduced into the production process as high-quality products and base metals. The ACROBAT process aims to recover more than 90% of the critical raw materials.
Partners combine expertise in ACROBAT
- Accurec will collect, dismantle and pre-treat the batteries with a process that is tailored to an input of LFP batteries
- ENEA will study the electrolyte valorisation with the aim to recover the organic solvents and the lithium-containing salt.
- Fraunhofer ILT develops continuous in-line characterization of the battery-active material to ensure its quality for the next recycling steps.
- VITO and SOLVOMET provide the recovery of graphite by means of a physical separation process
- SOLVOMET ensures the recovery of lithium and its conversion into valuable battery-grade lithium hydroxide monohydrate
- VITO recycles used LFP cathode material into new high-quality LFP material