Unique test lab for more sustainable concrete
The production of concrete, largely through the manufacture of cement, is responsible for 5 to 8 percent of global greenhouse emissions. In order to bring these immense emissions down, there is an urgent need for new concrete mixes based on alternative raw materials. These could be recovered (‘secondary’) minerals from waste streams, for example. VITO now has a versatile, state-of-the-art lab for testing these alternative concrete mixes since late 2021.
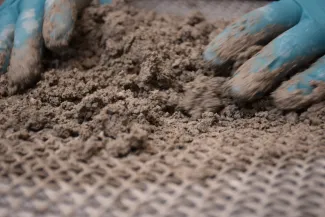
Circularity is a crucial concept in making the construction sector more sustainable. By starting to recycle and reuse construction waste from demolished or restored buildings as far as possible, the sector’s environmental impact can be reduced. Moreover, construction materials can absorb waste streams from other sectors, such as slag from metallurgy or mining waste. By revalorising components from those waste streams, the need for primary raw materials can also be limited. Recovered raw materials can partially replace aggregates and cement, for example – the two major components of concrete. Cement in particular is a ‘difficult’ component due to its immense climate impact: its production not only uses a lot of (fossil) energy, but also directly releases CO2.
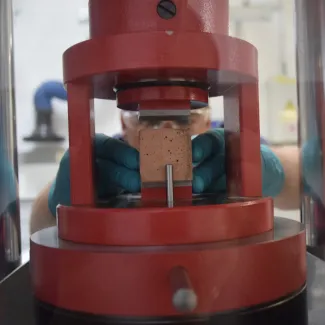
Unique expertise on recovered materials from waste streams
Using recovered minerals from construction waste streams as replacements for cement, known as supplementary cementitious materials (SCMs) is a route being investigated at VITO. ‘We’re looking for a destination for these secondary minerals, as they’re known, and it seems obvious that we should look to concrete for that in the first instance,’ says Arne Peys from VITO. He and his team have had a comprehensive lab for testing concrete, designed and assembled in-house at VITO, since late 2021. The concrete can be studied from all possible angles here: from mechanical properties such as sturdiness and durability (for how long will the concrete remain firm?) to more practical matters such as applicability (how easy is it to pour?). The test results are then used to draw a comparison with conventional types of concrete.
The main section of VITO’s ‘concrete lab’ is housed in a 150-square-metre space. This is where the largest equipment is kept for mixing, pouring or compressing the concrete and letting it harden, studying it continually very close by. More specialist tests are carried out in two adjacent labs. ‘The lab isn’t actually new,’ says Warre Van Dun from VITO. ‘We already had testing equipment, but it was smaller and more limited, and the devices were spread across several locations at VITO as well. That wasn’t working very efficiently. Now, we have some large and specialist equipment that puts us alongside the top labs.’ One of the concrete lab’s strengths is that – precisely thanks to the range of testing equipment it brings together – it is so versatile. This allows other construction materials besides concrete to be investigated as well, such as the sustainable Carbstone clinkers (an innovation from VITO, among others) that are made from steel slag and CO2 from emissions. But what makes the lab truly unique is the knowledge and expertise in the use of recovered materials and raw materials (such as minerals) from waste streams. The concrete lab’s team is also well-practised in extracting valuable metals from construction waste streams. ‘When I started at VITO, this was still where the focus was,’ says Van Dun. ‘Along the way, however, we started focusing more on the potential of the matrix, as it’s known, namely the large volume of material that remains after extraction of the valuable elements. This shows the potential of waste streams from construction, as well as from other sectors such as the metallurgical industry and mining.’
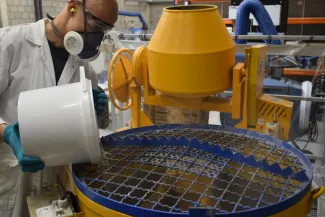
Sustainable concrete with better properties than those of normal cement
A test cycle at the concrete lab takes a minimum of 28 days. This is the time that concrete needs to fully harden and gain its optimum properties. During that period, the condition of the concrete will be assessed at set times, for example two days and seven days after it has been poured. ‘That’s the time after which you can stand on it and the time you can drive on it, respectively,’ says Peys.
The addition of SCMs could have a major influence on a concrete mix, even if it still partially consists of conventional (Portland) cement. ‘Some cement replacements are chemically inert or very mildly reactive, while others react very strongly with the cement and the aggregates,’ says Hadi Kazemi Kamyab from VITO. ‘It’s even possible that SCMs will produce a concrete mix with better properties tthan those of normal cement. Of course, that’s absolutely brilliant if your focus is on sustainable concrete.’
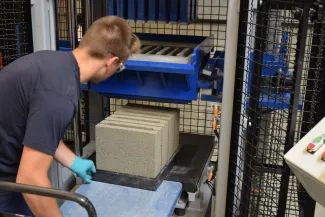
Who is knocking on the concrete lab’s door?
‘We carry out tests for both internal VITO research groups and external clients,’ says Peys. ‘They generally come to us for more specific, specialist questions. A company wants to investigate whether a particular residue from its production processes could be used as an SCM, for example. Or a concrete manufacturer is searching for alternative raw materials because they fear the availability of current ones might be at risk.’ In this context, it is important to note that the price of Portland cement has risen considerably in recent times.
Companies can also approach VITO’s concrete lab for tests on alternative aggregates (instead of sand, for example, which is often used at present). It is also working together with industry on a project around reuse of aggregates, again originating from construction waste. More and more companies are on the lookout for alternatives to this as well. Van Dun: ‘Due to the current scarcity of raw materials, we’re even seeing secondary raw materials sometimes being cheaper than primary ones.’