Upcycling mining waste into raw materials for concrete
Although we don’t immediately associate it with our continent, Europe still has a lot of mining activity. Nevertheless, mining metals such as copper, nickel and zinc produces large quantities of mineral waste - so-called tailings. Because this waste is mainly sent to landfills, it has a large environmental impact. The Horizon 2020 project NEMO, that ended late 2022, researched, developed and demonstrated solutions in this regard. VITO was also involved in the part of the project on recovering the mineral fraction of mining waste, working closely with ResourceFull. Together, they developed three different, ‘circular’ concrete mixes.
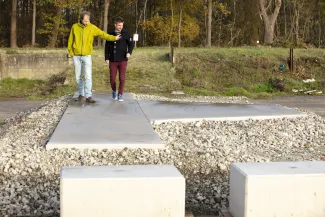
Every year, mining activities in Europe generate 700 million tonnes of waste. These ‘tailings’ remain after the ores being mined have been extracted. They have a primarily mineral composition (similar to stone and sand) and are usually dumped in landfills. These landfill sites are often lakes, as tailings tend to have a powdery texture whereby they can easily dissipate.
Unfortunately, mining waste contains a range of harmful components for the environment and human health (including heavy metals) that can enter the soil and groundwater via leaching and run-off. But storing tailings in an environmentally friendly way, for example by encapsulating them, is labour-intensive and therefore expensive, and requires long-term monitoring.
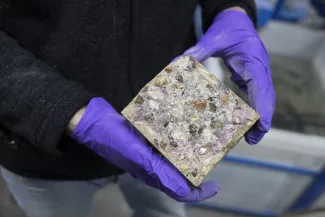
Alternative raw materials for concrete
Of course, this runs counter to the idea of circularity currently advocated by the European Union. The European NEMO project was therefore launched in early 2018, with the aim of finding circular solutions for tailings. The project was based on three principles: extracting leftover metals, isolating harmful and hazardous components, and upcycling the mineral fraction into raw materials for building materials. VITO and ResourceFull were also involved in the latter principle. ResourceFull is an SME specialising in the development of building materials based on industrial residual flows.
‘Producing concrete has a substantial climate impact, primarily through the manufacture of cement, which releases huge amounts of CO2’, explains Thomas Lapauw, CTO of ResourceFull. ‘By making concrete production more sustainable, large climate gains can be made.’ Currently, residual flows from the metallurgical industry, such as steel slag from blast furnaces, are already being used as alternative raw materials for concrete. However, the potential of mining waste, i.e. the mineral fraction, is many times higher. ‘But it is also much more challenging, partly because tailings have limited chemical reactivity. As a result, using it as a cement substitute is not that straightforward.’ Within the NEMO project, experts from VITO and ResourceFull jointly developed a method to increase the reactivity. They also worked out how to remove substances from the tailings that effect the properties of the concrete mix and can be harmful to humans and the environment, such as pyrites. If this is not possible, they can also set limits on the concentrations of these substances.
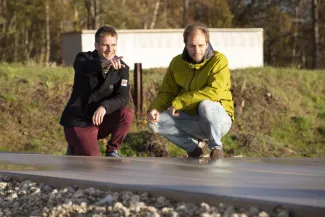
A new car park for VITO
As a demonstration within the NEMO project, three different concrete mixes were developed, which can be used in various applications. These were ready-mixed concrete (the most common concrete we see transported on the road by the typical concrete mixers), precast concrete (produced in NEMO in the form of slabs) and concrete bricks (for pavements, among other things). Each time, tailings were used as a cement substitute, although there was still cement in the concrete. ‘We can currently replace up to one third of the cement. In theory, it is possible to completely replace the cement, but this depends on the composition of the tailings.
The first application of the partially circular concrete mix took place at VITO’s Balmatt site in Mol in September 2022. Part of the new car park was cast using it. To monitor the quality in the longer term, some blocks were also cast that can later be examined more closely.
As part of the NEMO project, VITO also looked into valorising tailings into aggregates, which after cement are the main raw material of concrete. ‘We use the fine, powdery components of tailings as an alternative to sand and stones,’ explains Arne Peys from VITO. The research is being conducted in a new pilot installation for producing ‘artificial’ aggregates, which has a capacity of one tonne per day. VITO is in fact taking a broad look at valorising mineral waste streams into building materials. ‘We are targeting a wide range of applications, from high-grade cement replacements to low-grade fillers.’
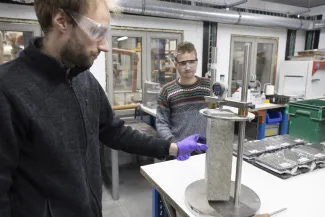
Logistical obstacles
With the completion of the NEMO project, it has been proven that more circular production of concrete, by valorising mineral mining waste, is possible. ‘The valorisation meets the technical and also environmental and health requirements,’ confirms Liesbeth Horckmans of VITO. It’s now up to industry. Ideally, a mining company would work together with a concrete producer. Unfortunately, this is usually not so straightforward in terms of logistics. ‘A lot of mining waste is produced in northern Europe, and because it is so heavy, transporting it over long distances is unlikely to be profitable.’ One exception is a mine near Dublin, in Ireland, one of the three case studies in the project. There are many local concrete producers in the area around that mine.
Comprehensive valorisation of tailings could make European mining a lot more sustainable. This could be a strength, as Europe seeks to become more independent in more and more areas from imports of raw materials, especially from countries with dubious regimes. ‘Moreover, demand for critical raw materials continues to grow,’ explains Peys. ‘We still have large reserves in Europe. More sustainable mining can therefore help make mining operations in Europe more acceptable among the public.’
The NEMO project was supported from the European Union’s Horizon 2020 programme, under agreement number 776846.

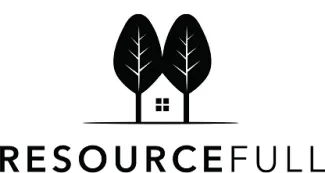