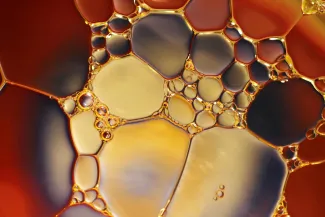
ISRO: membrane filtration as a large-scale solution for the repurposing of organic solvents
The ISRO project stands for Implementation of Solvent Recovery in the edible oil industry. Over four years, we examined how organic solvents can be repurposed in industrial processes based on membrane filtration, specifically through OSN (organic solvent nanofiltration).
Membrane filtration at an industrial scale: a challenge
Used organic solvents are a major source of waste in the industrial industry. Research shows that membrane filtration is a promising technology to recycle these solvents.
For instance, a previous project, EEMBAR (Energy Efficient Membrane Based Acetone Recovery), uncovered that organic solvent nanofiltration (OSN) can reduce the energy usage of acetone extraction by about 50%. Although EEMBAR demonstrated the proof of principle, the difference between small-scale experiments and the further development towards larger, industrial scale proved more complicated than we expected.
The main challenges were the specific nature of the plant-based oils, the relatively high oil concentrations that the membrane has to process and the impact of that in a large-scale transfer. As it was clear that this concept could be optimised to become a solution that meets the expectations, ISRO was set up for future research.
Repurposing organic solvents thanks to polymers and ceramic membranes
ISRO examined how solvents can be repurposed with the help of OSN within two different applications.
- The first application continued the work of the EEMBAR project and the integration of OSN in the distillation process at Bunge. That integration would allow the process to become more energy-efficient and create the option to increase the capacity at a lower cost and smaller carbon footprint than their current distillation process.
- The second case examined a rather unknown application: the recovery of a high boiling point solvent used by TUSTI to clean plastic fryer oil packaging. For TUSTI, using OSN would mean the solvent can be reused immediately. That would lead to considerable savings in transport costs, and it would make TUSTI’s biodiesel process more efficient by repurposing the extracted oil fractions.
For both applications, we developed and compared polymer and ceramic membranes. The most promising membranes were selected based on various criteria and evaluated at a pilot scale.
Useful insights and next developmental strides
The OSN applications at Bunge and TUSTI provided us with insights into the possibilities of membrane filtration at a large scale.
Tests on an increasing scale demonstrated that repurposing TUSTI’s solvent is technically possible with ceramic and polymer membranes. Additionally, it showed that the repurposed solvent can be used again in the plastic cleaning process. Moreover, the extracted oil fractions can be used to create biodiesel.
At Bunge, both polymer and ceramic membranes were tested at a pilot scale to find the most suitable circumstances. Overall, the acetone separation went as expected, but the membranes became fouled over time. For polymer membranes, we were able to develop an efficient cleaning cycle. As for ceramic membranes, we were less successful.
Something that made it more difficult to model the systems was, among others, that the lifespan of the membranes was still relatively unknown. Besides, we need more research on the fouling of ceramic membranes. Follow-up research with longer pilots can offer more insights on this.
VITO’s role in ISRO
- Developing modified ceramic membranes, including the upscaling of the most promising of the selected membranes.
- Designing efficient separation protocols by testing ceramic and polymer membranes at the lab scale.
- Executing pilot tests with selected membranes and modules on real processes and in relevant circumstances.
- Assessing the robustness, cleanability and performance of the membranes in the long run.
Funding
This project was backed by, among others, the Energy Top Sector of the Ministry of Economy and Climate.