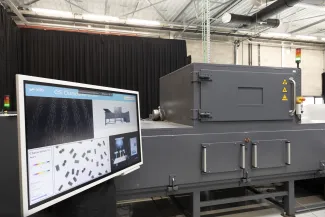
Characterise-to-Sort: find valuable materials in your waste stream
Heterogenous waste streams often hide valuable materials, such as batteries, copper, aluminium… Thanks to Characterise-to-Sort (CtS), an innovative piece of technology VITO created, you can easily recognise these materials – allowing you to recycle more efficiently. Time-consuming – and pricey – chemical analyses won’t be necessary.
How does the CtS technology work?
The process is similar to an airport baggage scanner. We put waste particles on a conveyor belt and screen them with a colour camera, a 3D laser scanner and X-rays. The device combines machine learning and artificial intelligence to recognise the individual particles. Each particle is given certain parameters like material class, shape, texture, and mass.
This way, you can quickly get reliable data on the complete material or waste stream. Complex material streams can be sorted automatically based on this information.
Why was this technology developed?
More often than not, waste is not recycled in the most efficient way. Until you know what’s in your waste stream, you cannot recycle efficiently. With CtS, you can quickly determine:
- how many different materials are in your waste stream
- how big the particles are and what shape they have
- what the nature and mass of each particle is
- what the value of your waste is.
VITO wants to accelerate the transition to a sustainable world, and an important part of that process is the transition towards a circular economy. Repurposing valuable materials optimally is essential to that process. By developing technology like CtS, we can contribute to that.
The benefits of this way of waste characterisation
This way of waste characterisation offers companies several benefits:
- quick results
- an analysis of your complete waste stream
- a non-destructive way to analyse materials in your waste stream
- new insights and material knowledge.