Enzymes help chemical industry to become greener
To reduce its environmental and climate impact and also to have a more efficient, economic and safe production, the European chemical industry must reinvent itself. One way of doing this is to switch to new process technologies. The enzymatic route is a promising track, in which biological catalysts are used in the production of chemicals for, among others, the pharmaceutical, food, agro and cosmetics industries. Within the European INCITE project, VITO works together with chemical company Oleon on the route to industrial applications.
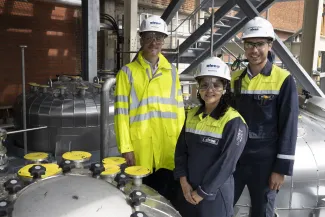
Esters (organic compounds) are an important group of chemical compounds in the chemical industry. In order to produce them, high temperatures and pressure (and thus robust chemical reactors) are often required. The production also often requires solvents, which usually have a high environmental impact. Finally, this 'chemical' method of production can also affect properties such as colour and odour in end products, something that is preferably avoided in both the food and cosmetics industries. If there is an alternative to produce esters in a more natural and sustainable way, it would be very welcome in the chemical industry.
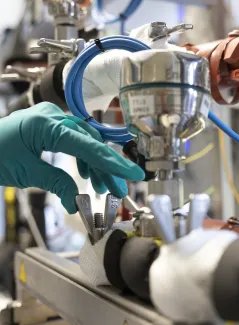
Enzymatic route
This alternative can be found in enzymatic processes. Enzymes are nature's catalysts. In the form of often complex biomolecules, they catalyze the chemical reactions under mild temperature and pressure conditions. These reactions typically proceed without the need for auxiliary chemicals and solvents, offering routes that involve considerably less steps and generate less waste than conventional organic syntheses.
Due to the scarcity of energy or raw materials and the search for renewable raw materials, there is now a strong interest in the 'enzymatic route', which was never fully rolled out until early 2000s. Development of enzymatic solutions for large scale processes has then started to expand. VITO has been involved in this research for many years, including the LipaMetics project supported by Catalisti, which focused on the solvent-free enzymatic production of chosen esters for use in cosmetics and animal feed.
One such ester, called isopropyl palmitate, was produced so well in the lab that it was decided to set up an industrial demonstration. The goal? The production of several hundred litres of this component via the enzymatic route to pave the way for commercial exploitation. This demo installation is now part of a larger and more international follow-up project, which started in 2019 and is called INCITE.
The demo plant for the enzymatic production of isopropyl palmitate is about to be completed at the Oleon site along the Albert Canal in Oelegem. Oleon, a chemical company specialised in the processing of animal and vegetable oils, was and is involved in both LipaMetics and INCITE. Now that the plant is almost ready, we will soon proceed to the first large scale test runs and the first production of isopropyl palmitate,’ says Yann Raoul, Collaborative Project Specialist at Oleon. ‘We will then also highlight what the benefits of the enzymatic route are over the conventional route.’
Two industrial demonstrations
Oleon is the coordinator of the INCITE project, in which besides VITO six other companies and knowledge organisations from Belgium, Germany, France and Italy are participating. The Flemish chemical company is responsible for the oleochemical part of the project. This should lead to a solvent-free, enzymatic synthesis of natural esters as ingredients in human and animal food, in cosmetics (personal care products) and in crop protection products. Another part, the agrochemical track, involves the demonstration of an enzymatic production of chemicals for use in crop protection as insecticide precursors. The Italian chemical company Endura (from Ravenna) is responsible for this. The oleochemical demo plant at Oleon will be completed at the end of 2022, and the agrochemical demo installation should be operational by mid 2023, which is also the end year of the INCITE project.
The expansion of the enzymatic route from lab to industry scale is quite a challenge. Enzymes are active, complex biomolecules that enable or accelerate specific chemical reactions,’ says Yamini Satyawali of VITO. They are biodegradable and often have very specific properties, so you need to know in which processes, and under which circumstances you can use them. In addition to the enzymes’ function, VITO also investigates within INCITE how the water produced during the esters’ production can be eliminated. We do that with a membrane technique called pervaporation’, says Satyawali. Pervaporation is a combination of permeation and evaporation. ‘With this separation technique, the formed water is separated from the esters. The continuous elimination of the water results in increased process efficiency and makes this technology economically very interesting for the industry.’
The progress that has been made, first in LipaMetics (which started in 2015) and now in INCITE, looks impressive. What started as the production of a few tens of grams of finished product quickly became several kilograms. And soon several tons. The end product (isopropyl palmitate) is already available for testing. Companies that want to use it in their R&D labs can apply for a sample on the INCITE website. ‘We really want to move forward now,’ says Raoul. ‘We’ve been delayed by corona and by raw material scarcity. We are now eager to demonstrate the added value of the enzymatic production method to our industrial customers.’
INCITE is supported by the European Union’s Horizon 2020 research and innovation programme under grant agreement N° 870023. The project is also part of Processes4Planet (A.SPIRE), the European agenda to make the European chemical industry climate neutral and circular. The transfer of newly acquired knowledge and expertise is important in this respect, which is why this element is also addressed within the INCITE project. Courses and trainings focusing on enzymatic process technology are offered to both chemistry students and professionals.
This project has received funding from the European Union’s Horizon 2020 research and innovation programme under Grant Agreement No. 870023.