European innovation and testing environment for membrane technology
Innovative membrane technology tailored to industrial customers. That is what the European INNOMEM project aims to help ensure. About 30 companies, universities and research centres work together on improving and scaling up existing membrane technologies, tailored to the specific needs of industry. For one of these ‘showcases’, i.e. optimised membranes for waste water treatment, VITO is responsible together with the Danish company Liqtech.
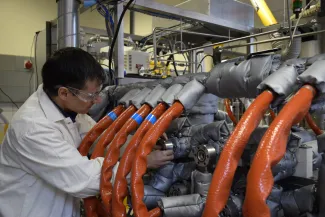
VITO has extensive expertise in membrane technology. One of its strengths is optimising membrane surfaces by linking all kinds of functional molecule groups to them. This is done down to nano level, inside the pores of the membranes. These so-called nano-enabled membranes have much better properties than untreated membranes. In wastewater treatment processes, for example, they are less likely to encounter deposits of dirt particles. They also provide a more stable flow and, moreover, they also last longer, resulting in a less frequent replacement of the membrane.
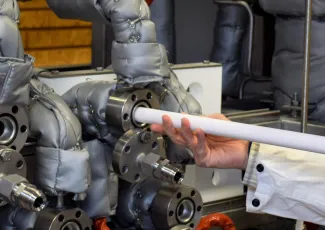
Wanted: the right membrane technology
VITO has its own pilot installation on its Mol site to treat or graft ceramic membranes in this way. This installation has recently been scaled up in order to bridge the gap between R&D and industrial application. The scaling up was carried out within the framework of the European INNOMEM project, in which around thirty companies and knowledge institutions (including VITO) work together on the improvement and scaling up of various membrane technology development and production lines. “We are building a real innovation and testing environment for membrane technology on a European scale,” says Anita Buekenhoudt of VITO. “This involves a wide range of materials for membranes (from polymer to ceramic to metal), various surface treatments, different geometries and of course a wide range of applications. The ultimate goal is for companies in need of a membrane solution to find exactly what they are looking for: the perfect technology that is also sustainable and cost-effective.”
In the first half of INNOMEM, which started in May 2020, the focus was mainly on scaling up the fourteen pilot installations that the project focuses on - including the membrane installation of VITO. The project then moved into a new phase at the end of 2022, which zoomed in on applications. Through a recent open call, European companies were encouraged to come up with concrete problems for which innovative membrane technology could provide solutions. This led to a selection of seven so-called ‘demo cases’ in which a specific case will be central and for which smaller collaborations are currently being set up with certain project partners. To stimulate companies to explore the possibilities, around ten ‘showcases’ were elaborated within INNOMEM. In one of these showcases, the membrane experts from VITO worked together with another project partner, Liqtech, an established Danish company that offers sustainable filtration solutions for liquids and gases based on membrane technology. In their showcase on treated ceramic membranes for wastewater treatment, the strengths of Liqtech and VITO come together. This is not their first collaboration, by the way. “We have already carried out projects together with VITO,” says Victor Manuel Candelario Leal of Liqtech. “For example, on the optimisation of oil-containing waste water in the Netherlands. The advantage of this previous collaboration is that we know each other’s strengths well.”
Water purification on ships, in power plants, or in metal processing
In their showcase, Liqtech and VITO want to demonstrate the better performance of treated ceramic membranes for wastewater treatment. “We are looking at how we can increase the flow, in this case the water flux,” says Candelario. “Or we investigate the effect of even smaller pores on the functioning of membranes, or of adapted mechanical properties on their lifespan.” The longer membranes last in industrial processes, the better, because replacing them often requires the processes to be shut down, which of course should not happen too often. It is no surprise that more performant membranes also save costs for the user - which is why the financial aspect is also taken into account within INNOMEM.
The demand for improved wastewater treatment is frequently requested by various companies. For example, it came from a company that develops systems to purify wastewater on board ships so that it can be safely discharged into seas and rivers. So-called scrubbers are also used by power plants to discharge or reuse their cooling water. Similar wastewater is also produced by companies that machine-cut metal. Candelario: “In this case, we focus on the separation of oil-and-water emulsions, where the oil comes from lubricants. In the separation of such emulsions, the membranes quickly become dirty and clogged, which reduces their lifespan. Having to clean them time and time again is not an attractive option.’
A better option is to make the membranes more inert, so that particles such as oil are less likely to stick to them. Liqtech and VITO achieved this by grafting LiqTech’s ceramic membranes made with an active layer based on zirconium oxide, at VITO. The innovative treatment (recently transferred to spin-off A-membranes) was applied to about ten membranes in the VITO pilot plant. Tests with the membranes showed that they are not only more resistant to dirt, but also allow for a higher water flux. Buekenhoudt said, “This means that the membranes can be used more effectively, which will reduce the amount needed. This also reduces costs.”
In addition to this showcase, Liqtech is also involved in another one. And while the project partners of INNOMEM - the cream of the crop in Europe working on innovative membrane technology - are still busy with the new demo cases (VITO is involved in 2 of the 7 cases), a new open call will be launched in the spring of 2023 for new problem areas regarding concrete membrane applications in companies.
When INNOMEM ends in 2024 and European subsidies expire, a sustainable partnership will offer the same services to industry. “The goal of this project is to have an independent, viable organisation in Europe so that companies can easily find the right membrane technology, as well as the right expertise to help answer their specific questions, or even the right installations to scale up their own membrane developments,” said Buekenhoudt.