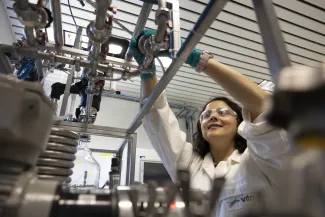
Enzymatic process intensification for more efficient chemical processes
Seeking environmentally friendly and efficient chemistry solutions? Consider natural catalysts like enzymes. They allow you to significantly reduce waste, lower energy consumption, and minimise the production of challenging byproducts. VITO offers the expertise, equipment and infrastructure you need to design and implement these in your processes.
Why opt for enzymatic conversions over chemical conversions?
Enzymatic conversion harnesses the specificity and efficiency of enzymes to convert substrates into desired products with high selectivity and minimal side reactions. Enzymatic conversions play a pivotal role in producing pharmaceuticals, fine chemicals, biofuels, and ingredients for the food industry, offering a sustainable alternative to traditional chemical synthesis.
- Higher selectivity and specificity: Enzymes provide remarkable substrate and product specificity, reducing the need for complex purification steps.
- Milder reaction conditions: Enzymatic processes typically occur at ambient temperatures and neutral pH, minimising energy consumption and harsh chemicals.
- Reduced environmental impact: Enzymatic reactions generate fewer byproducts and hazardous wastes.
- Biodegradability and safety: Enzymes are biodegradable and generally non-toxic, contributing to safer and more sustainable manufacturing processes.
- Ability to catalyze complex reactions: Enzymes can facilitate intricate biochemical transformations that are difficult or impossible to achieve with traditional chemical catalysts.
Typical applications of enzymatic catalysis
- Synthesis of fine chemicals and intermediates
- Synthesis of chiral molecules
- Food processing and ingredient modification
- Selective functionalisation of molecules
- Development of pharmaceuticals and active pharmaceutical ingredients (APIs)
Industrial examples of enzymatic catalysis
Chemical industry: production of acrylamide
Acrylamide, a crucial monomer for polyacrylamide production, is traditionally synthesized using a copper catalyst. However, enzymatic catalysis using nitrile hydratase has revolutionised this process. The enzyme-catalyzed reaction occurs under milder conditions, significantly reducing energy consumption and hazardous waste generation. This enzymatic method also offers higher selectivity and yield, demonstrating the efficiency and environmental benefits of biocatalysis.
Food industry: high-fructose corn syrup production
In the food industry, the enzymatic conversion of starch to high-fructose corn syrup (HFCS) employs amylase, glucoamylase, and glucose isomerase. These enzymes work sequentially to break down starch into glucose and subsequently convert glucose into fructose. The enzymatic process is highly specific, ensuring high purity and yield of HFCS while operating under mild conditions that preserve the nutritional quality of the product. This approach also minimises the need for harsh chemicals and extensive purification steps.
Personal care ingredients: sustainable esters
Oleon has inaugurated Europe's most innovative oleochemistry plant in Oelegem, near Antwerp, specialising in sustainable enzymatic esterification for the food and cosmetics industries. This facility reduces CO₂ emissions by over 40% and waste production by 60%, marking a significant advancement in eco-friendly industrial processes. Annually, it will produce 3,000 tonnes of sustainably made esters, distributed globally via the Port of Antwerp.
How does VITO support you?
VITO helps you design new enzymatic processes and intensify existing ones. You can count on support from lab to production scale:
- Biocatalyst characterisation
- Development of a digital twin process model, allowing simulation of problems and solutions
- Kg scale production of your product, ready for quality testing
- Development of economic models supporting your processes
- Pre-commercial pilot scale production
- Engineering support for commercial production
Optimise your processes with enzymatic intensification
Discover how you can save costs and improve efficiency. Contact Marzio Monagheddu for more information.
Questions about enzymatic process intensification
Enzymatic process intensification can be used by the pharmaceutical, cosmetic, food and feed, flavour and fragrances, fine chemical industry and others. It’s suitable for any company that is looking to design and optimise an enzymatic process or find a biobased alternative to an existing chemical processes. It’s also useful for companies that operate in biocatalyst development and that are in need of a bioprocess development or upscaling partner and for technology developers or suppliers.
Yes. Either a single membrane filtration step or a cascade of membranes can be used to obtain oligomers with a specific molecular weight range. Examples are tailor-made peptides and oligosaccharides.
The price of enzymes decreased significantly in the last years, thanks to the increase in commercial volume available on the market and number of suppliers. Nowadays their price is not far from other specialised catalysts, and their advantages in terms of specificity, mild operating conditions, and environmental friendliness can offset their initial cost in many applications.
Yes. Current commercially available supported enzymes are easy to handle and have a lifetime comparable to many heterogenous catalysts.