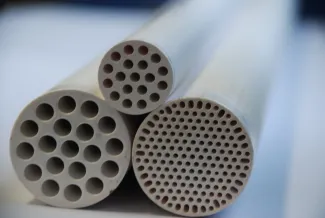
Membrane technology
In a world that is trying to reduce its carbon footprint, where major chemical companies have pledged to achieve ambitious sustainability goals, the great potential of membrane filtration is unknown to many.
Are your processes aligned with the European sustainable transition targets? Membrane technology represents a robust tool to achieve these targets and with the help of VITO you can make your investments future-proof, hence increasing competitiveness. VITO provides independent science based contract research services, helping you to select the most sustainable and economically viable separation process to reach your business goals.
What is membrane filtration?
Membrane filtration is a mild, non-destructive and energy-efficient separation technique that represents a sustainable alternative to conventional separation processes, such as distillation and evaporation, and is complementary to crystallisation.
A membrane is a semi-permeable barrier between two liquid phases. When a driving force (pressure, concentration, temperature) is applied, the components of the feed stream are retained or permeated depending on their interaction with the membrane.
Energy-efficiency is embedded in the DNA of all the membrane processes: e.g. pervaporation which is comparable to distillation but much more energy-friendly, combines permeation and vaporisation.
The separation efficiency of a membrane process is defined by the flux through the membrane and the selectivity or capability of the membrane to retain or let through specific components.
Carefully selected process conditions and cleaning protocols allow to address fouling issues, ensuring a long lifetime of the membrane, reducing the cost of use, adding to your ease of mind.
Membranes allow for several unit operations. The most common ones are concentration, purification and solvent exchange.
The qualifying features of any membrane process are:
- Isothermal: there is no change in temperature, resulting in energy saving and allowing for separation of labile compounds
- No additives: nothing is added, the feed is separated as it is. This makes membrane separation particularly suited for highly regulated products
- Scalability: scale up of membranes is mostly performed by adding modules that intrinsically reduce the risk associated with large scale-up factors
Why use membrane filtration as a separation technology?
Membrane filtration can give you the competitive advantage by significantly reducing energy consumption. It has potential for material savings and offers opportunities for your side and waste streams. Membrane filtration has a reduced footprint and process complexity, thereby minimising costs and impact on environment.
- Non-thermal, molecular scale separation
- Suitable for many unit operations, from concentration and purification of valuable compounds to solvent recovery
- Inherently energy-efficient, mild and scalable, offering a real sustainable alternative to classical separation technologies
- Enormous potential for intensification/debottlenecking of solvent-intensive processes regarding energy requirements, CO2 footprint, resource circularity, product quality/yield, productivity
- Extensive opportunities for both process and product innovation/improvement
- Widely applied and applicable across process industries, from pharma to oil and gas
- Readily available technology for separation toolbox of process chemists and engineers
- Number of industrial realisations increasing steadily, driven by established/emerging market players and a small but active research community
Membrane technology for your business
Would you like to use membrane technology to improve your processes and business? Are you looking for food-grade, GMP compliant and/or ATEX-rated pilot plant infrastructure to reduce the risk towards upscaling of your membrane technology innovation? We'd be happy to help you.
Which applications are suited for membrane filtration?
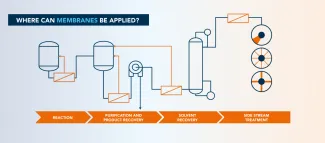
Reaction
Manage equilibrium reactions, increase catalyst TON, improve carbon economy, increase overall sustainability. These are just some of the challenges process chemists have to meet every day. With raised awareness for sustainability in chemical companies, these are challenges that require a specialised approach. In fact, membrane separation may offer new options, as has already been demonstrated in:
- High dilution synthesis
- Ring closing metathesis
- Oligonucleotides synthesis
- Enzymatic reactions
- Peptide synthesis
- Hydrosilylation of alkenes
- Alkyne hydration
- Suzuki coupling
- Mitsunobu reaction
Purification and product recovery
Membrane separation is new in the process development engineer toolbox. When you are considering evaporating a solvent, distilling a mixture, crystallising your product, you may want to look at membrane separation.
Isothermal concentrations, impurities removal, second crop from mother liquors, solvent switch, telescoping, counterion swap, homo catalyst recovery, API recovery are just some of the typical applications of membranes.
Solvent recovery
Most chemical processes require a solvent. Which is a double cost: when purchasing and when discharging. That’s why nowadays an increasing number of companies are equipped with a solvent recovery section. Solvent recovery is mostly performed by distillation that requires heat, which is becoming more and more difficult to source as well as expensive. Sometimes, membrane separation allows for a balance between economics and sustainability aspects, by enabling clean separations that are isothermal or can be operated with residual heat.
Side stream treatment
Environmental chemists and engineers typically have to deal with low budgets, large flow rates and a few components that can be non-biodegradable, environmentally hazardous etc. High flow rate, particularly when water is the main component, rules out distillation and evaporation for economical reasons.
This is where membrane operation can play a role. Thanks to the broad availability of water treatment membranes and the easy scalability you can address a wide variety of environmental challenges that could not be solved before.
Would you like to know more?
Our experts are happy to discuss how you could benefit from our innovations in the field of membrane technology. Fill in the form below and we'll get in touch.
Frequently asked questions
Membrane filtration is a mild, non-destructive and energy-efficient separation technique that represents a sustainable alternative to conventional separation processes, such as distillation and evaporation, and is complementary to crystallisation.
Membrane filtration can give you the competitive advantage by significantly reducing energy consumption. It has potential for material savings and offers opportunities for your side and waste streams. Membrane filtration has a reduced footprint and process complexity, thereby minimising costs and impact on environment.
- Reaction
- Purification and product recovery
- Solvent recovery
- Side stream treatment